Black is black
In high-end applications such as the automotive industry, very deep blacks with a blue undertone are especially desirable. However, the high surface area carbon black pigments needed to achieve this can be difficult to disperse, which limits the colour strength that can be achieved. Choosing the correct dispersant and optimising its usage are crucial for achieving the best colour strength. A Paint Research Association (PRA) project involved identifying the best performing dispersant for a ‘high colour’ carbon black pigment, out of three potential candidates.
After selection of the three candidate dispersants, a series of optimisation steps was carried out in PRA’s formulation lab, to ensure that the maximum potential performance was achieved for each dispersant. These included:
- Dispersant concentration optimisation
- Pigment concentration optimisation
- Milling time optimisation and colour measurement
The optimum concentrations of dispersant and pigment were determined via ladder studies, using a dual asymmetric centrifuge mixer, with 1.2mm ceramic beads to aid pigment dispersion.
The optimum milling time and colour performance properties were determined using a bead mill equipped with a thermally controlled vessel and a double disk impeller. The milling media used were 1mm ceramic beads, and the milling was carried out for five hours in total. Various tests were carried out to assess the degree of pigment dispersion. Colour performance was tested in a high gloss, waterborne polyurethane coating, tinted using the pigment concentrates prepared in the bead mill.
Investigations found that Dispersant 1 had the highest jetness, reaching a very high maximum value in three hours. Dispersants 2 and 3 had lower jetness values, with Dispersant 3 having the slightly better colour performance of the two. All three dispersants had desirable positive (blue) undertone values, with Dispersant 1 again having the best performance.
The PRA also found that Dispersant 2 had the lowest ODC and the best viscosity reduction properties. This indicates a lower dispersant requirement and improved milling efficiency.
Depending on customer requirements, different candidates may be recommended: Dispersant 1 for the highest jetness, or Dispersant 2 as a potentially more economical option.
The PRA explains that it can be challenging to achieve optimum colour performance from high jetness carbon blacks and some organic colour pigments.
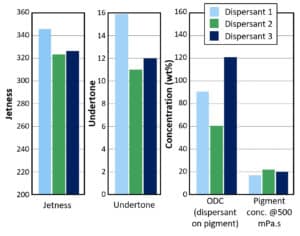
The colour strength of a black coating is measured as a ‘jetness’ value; a higher jetness corresponds to a perceived deeper black colour