Custom coating systems accelerate the use of exotic materials
Innovation in cutting-edge sectors such as defence, aerospace, biomedical, medical, and energy is driving the coatings industry to meet rising demand for higher component performance. As such, manufacturers increasingly use exotic materials because of their unique properties, including lightweight, extreme hardness, and the ability to withstand extreme temperatures and highly corrosive environments.
Applying such coatings is performed through chemical vapour deposition (CVD) systems that deposit exotic materials in gaseous form as thin film layers on substrates such as metal or glass. While such systems are already widely used for silicon carbide, graphite, and pyrocarbons, industry demand is increasingly embracing even more exotic and, in many cases, rarely (or even never before) deposited coatings such as iridium, tungsten, tantalum, hafnium carbide, zinc sulfide, boron phosphide, and titanium diboride.
In many cases, however, incorporating new exotic materials requires much more than modifying an existing CVD system. Instead, experienced system designers are tasked to provide custom systems that resolve challenges based on unique substrate with varying sizes, uniformity, throughput, and increasingly exotic materials.
A host of challenges can arise when working with exotic precursor materials in a CVD system, starting with the ability to handle each unique material. The process requires converting solid and liquid materials to the gas form required for film deposition. Venting vapours and off-gases must satisfy stringent ATEX environmental safety standards, while ‘extremely dirty vacuum’ conditions within the reaction chamber must be managed.
“For most companies, a zinc sulfide or titanium diboride coating is going to be outside of their scope,” says Sylvain Bentivegna, Managing Director and founder of MPA Industrie, a physical and chemical engineering provider of CVD coating systems and ceramics and fibre matrix composites based in France. MPA was recently acquired by global industrial process provider PVA TePla. The company has a 30-year history specialising in advanced material processing, including manufacturing specialised CVD reactors.
“Most CVD system designers are going to piece together a system from different providers of subsystem components such as reactors, pumps, off-gassing, and scrubbers,” says Bentivegna. “These systems are not designed from a ‘global’ perspective for the deposition of specific exotic materials.”
“The starting point for us is to create a highly integrated CVD solution designed and built to meet the specific requirements of the exotic material, whether the precursor is in gas, liquid, or solid form,” adds Bentivegna. “We are not limited by the material. When you master all the component parts of the technology, working with a new exotic material is relatively easy and can be performed safely.”
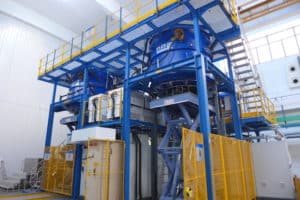
Custom equipment designed for the deposition of exotic materials allows advanced coating solutions and ceramic matrix composites to be utilized for applications in automotive, aerospace, defense, energy, and the farthest reaches of space
Vapour deposition (CVD/CVI/CMC)
CVD is a vacuum-based deposition method for producing high-quality and high-performance solid materials. By exposing a substrate to one or more precursor materials in gas form within a reaction chamber, the desired materials with their unique properties are decomposed and deposited on the surface of a substrate while in a vapour phase. The process must be carefully controlled to achieve the desired properties including the thickness of the film and to manage the volatile by-products which are produced. These must be carefully removed from the chamber through gas flow.
The breadth of CVD applications has grown well beyond its popularity in the semiconductor industry where thin films are used on silicon wafers. Today, smart phones require thin films made from graphene for flexible displays such as QLED displays, and for integrated sensing devices such as MEMS accelerometers. The aerospace industry uses hard coatings like titanium nitride and chromium carbide to reduce friction and wear on components, much as the diamond cutting tool sector relies on exotic materials for increasing hardness and wear resistance of drills and end mills.
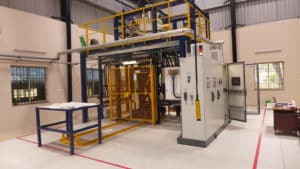
Experienced system designers provide custom systems that resolve challenges based on unique substrate with varying sizes, uniformity, throughput, and increasingly exotic materials.
In the energy sectors, CVD is used to produce gas diffusion layers for fuel cells, while Copper-Indium-Gallium-Selenide (CIGS) and Cadmium Telluride (CdTe) are used to create an absorber layer in thin-film solar cells. CVD coatings are also commonly applied in the medical sector to enhance biocompatibility and reduce wear in orthopaedic and dental implants.
Chemical Vapour Infiltration (CVI) and Ceramic Matrix Composite (CMC) are related processes that require many of the same system components. CVI is used to create carbon-carbon composites consisting of carbon fibres embedded in a carbon matrix whereas CMC is used to embed ceramic fibres in a ceramic matrix. Both are prized for being lightweight while providing high tensile strength, resistance to thermal stress and shock, and ability to withstand extremely high temperatures.
The applications for CVI and CMC include gas turbine shrouds and nozzle guide vanes; spacecraft heat shields, thermal tiles, aperture shields, and insulation; missile nose cones and control surfaces; aircraft brake discs and propeller blades; automotive exhaust components; industrial heat exchangers; ceramic cutting tools; and high-temperature furnace components.
Orchestrating a customised CVD solution
A CVD system is a highly orchestrated process that integrates complex component subsystems all of which need to be tailored to the unique properties of each material selected for vapour deposition. Principally, these include a reactor, vacuum pumps, treatments for the off-gases that are generated, and oversight through automation controls.
In-depth knowledge of how to extract and apply the desired properties from a wide range of exotic materials is first required. MPA uses specially designed gas engineering systems that can convert the exotic precursor materials to produce the gases needed for vapour deposition whether they are in solid, gas, or liquid form.
Hafnium and zirconium, for example, are among the exotic materials that are used in solid form. For these materials, MPA designed a metal chlorination process to create hafnium chloride and zirconium chloride tetrachloride. These gases can then be combined with a hydrocarbon such as propane to produce hafnium carbide and zirconium carbide.
“When a customer asks for an exotic material, we can propose a solution, because if we need a solid source, we have a solution,” said Bentivegna. “And if the engineering dictates a liquid source, we have a solution. If we need an inlet gas or we need to adapt the pumping system, we have a solution.”
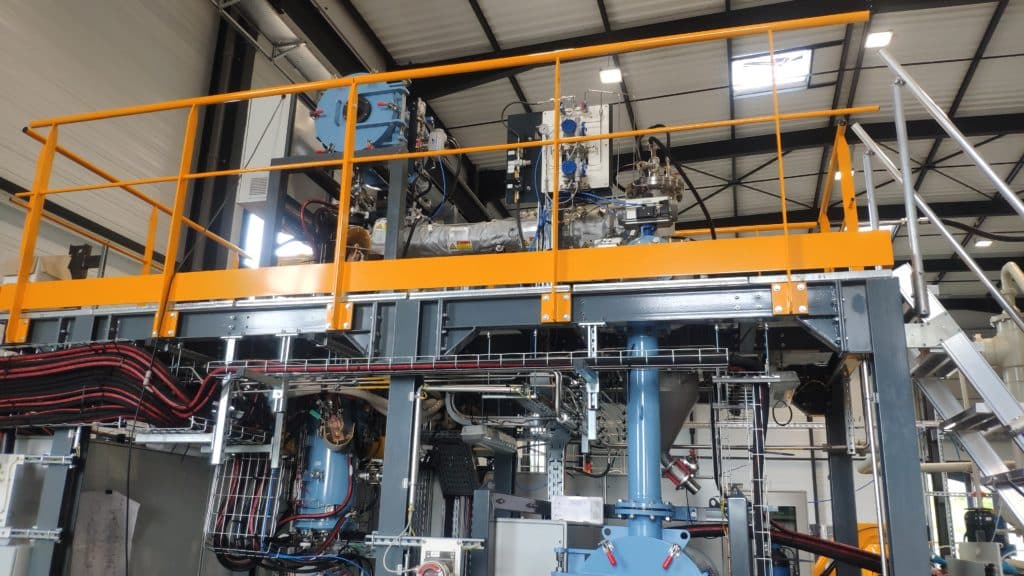
The starting point is to create a highly integrated CVD solution designed and built to meet the specific requirements of the exotic material, whether the precursor is in gas, liquid, or solid form.
Even a seemingly straightforward component like the vacuum pumps can be a challenge as the chemical vapour deposition process is very severe for pump components. A device between the reactor and the pumping system cleans the by-products of the vacuum. Dust and effluent made of corrosive materials make a CVD vacuum very “dirty” making the CVD process very hard on pump components. Most of the by-products are made of hydrogen chloride or hydrogen fluoride and need to be cleaned.
“If you have trouble and lose your pump, you lose your process. So, between reactors and pumps, we install subsystem for quenching gases, cropping solid by-products, or filtering by-products,” says Bentivegna.
All of these systems (CVD/CVI/CMC) require a stringent commitment to safety because of the presence of hazardous gases such as hydrogen chloride, hydrogen sulfide, phosphine, asin, and boron chloride. These gases are often toxic, corrosive and explosive. MPA supplies the gas cabinet with all the required safety devices (venting, gas detection) to adhere to ATEX Directives.
Throughout the CVD process, precise control of gas flow, temperature, and pressure is needed for the chemical deposition to occur and so SCADA systems are integrated for control and safety.
“Each time we develop a specific system for a new exotic material, we approach it is an R&D project,” says Bentivegna. “After each project the knowledge we gain supports future projects and research. The accumulation of specialized knowledge of system design continues to expand our capabilities [to customise systems for new exotic materials] in the future.”
To date the company has developed processes and equipment for an extensive number of advanced coating materials. These include TiC, TiN, Ti(CN), PyC, SiC, B4C, TiB2, BN, Al203, AIN,W, Re, ZrC, TaC, HiC, DLC, ZnS, ZnSe, and doped aluminising.
Anticipating that exotic materials will continue to play an increasing role to meet the demand for high-performance coatings, new industry collaborations are being formed to leverage specific areas of expertise.
MPA Industrie recently merged with PVA TePla whose industrial plant engineering business sought MPA’s expertise in industrial vacuums and work with exotic materials including silicon carbide (SiC) components and SiC layers for the industrial sector. MPA is now supported by PVA on a global level for service support and is growing rapidly.
“By merging with PVA, it has really allowed us to move more quickly globally,” said Bentivegna. Having focused on Europe and China, MPA is now focused on bringing their advanced materials processing expertise to the US, focused on industrial and aerospace sectors.
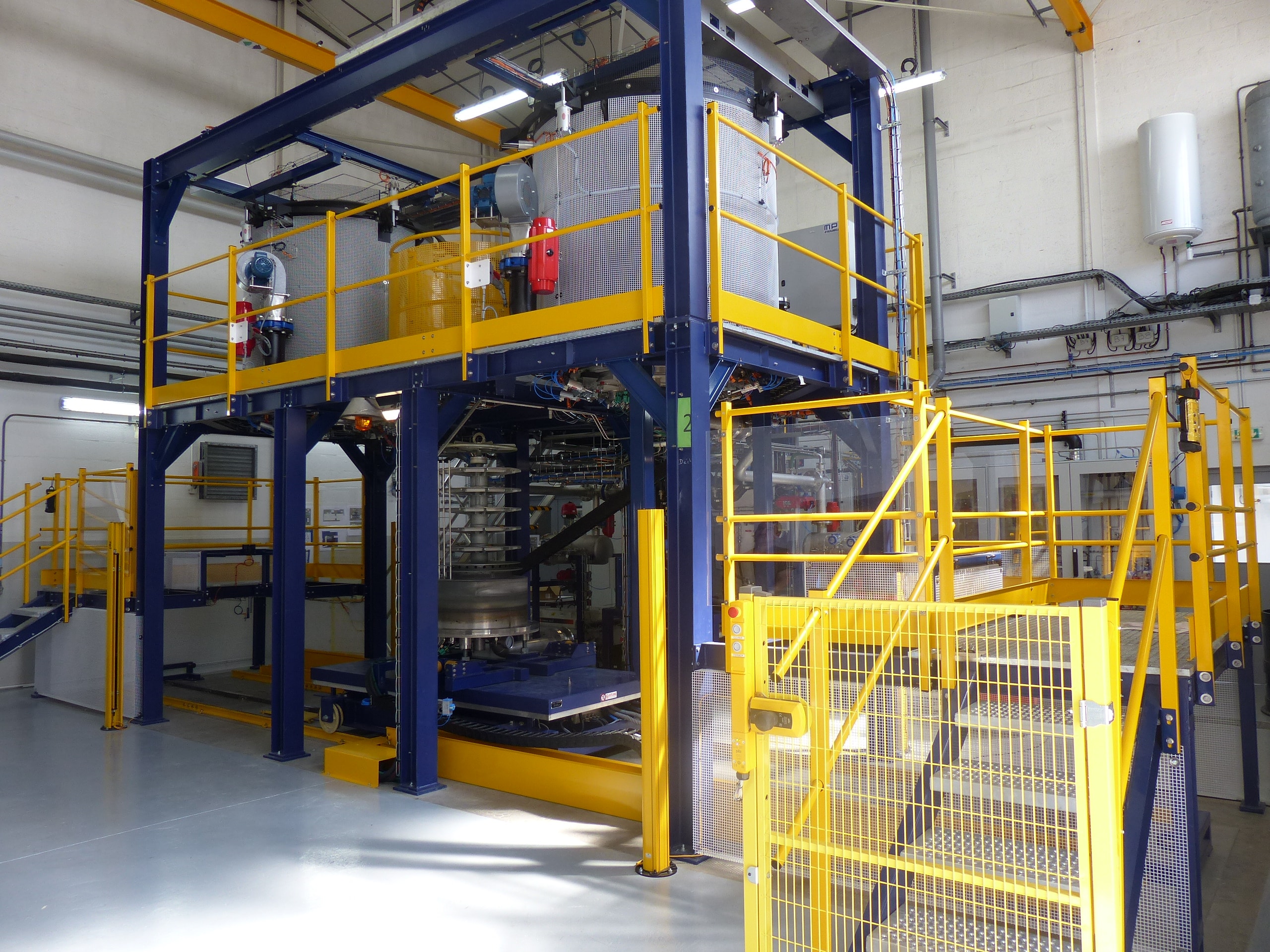
MPA uses specially designed gas engineering systems that can convert exotic precursor materials to produce gases needed for vapour deposition.