Making the solution fit the need
Finding the best paint for metal involves much more than picking a favourite colour. In addition to good adhesion and rust prevention, a metal coating must be equipped to meet force-dry, high slip, or high temp requirements in certain applications. To address these needs, Cortec offers two specialty versions of EcoShield VpCI-386, a high-performing water-based anticorrosion coating for industrial applications.
Two anticorrosion paints – three special features
EcoShield 386 FD is a water-based acrylic one-coat system that can be applied direct-to-metal (DTM) for protection in harsh, outdoor, unsheltered applications. It was specifically designed for fast-paced, force-dry applications, common in manufacturing environments. In addition to outstanding corrosion protection at 1.5-3.0 mils (37.5-75 µm) DFT (dry film thickness), EcoShield 386 FD force-dries in just 5-10 minutes at 150°F (65°C) and has good hot hardness. EcoShield VpCI-386 HT Slip Coating is another DTM water-based topcoat that offers excellent corrosion protection at 1.5-2.0 mils (37.5-50.0µm) DFT. It is heat resistant up to 500°F (260°C) or more (depending on colour) and improves surface slip. The coating is thixotropic and resists sagging and running during application. Both EcoShield 386 FD and EcoShield VpCI-386 HT Slip Coating are UV resistant and low VOC.
Where are force-dry, extra slip, high temp coatings needed?
Whilst it would be difficult to list all the industrial applications where force-dry, extra slip, or high temp coatings could be used, the following examples are excellent springboards for exploring options.
- Force-dry applications
Fast-paced manufacturing applications are the number one candidate for EcoShield 386 FD. Many spray or dip lines move so quickly that the parts pile up at the end of the line. This is bad news if parts are hot and sticky – they could easily adhere to each other and potentially damage the coating when components are pulled apart. EcoShield 386 FD, which is designed for force-dry applications and has good hot hardness, will reduce the risk of parts sticking together. This feature is a potentially huge advantage in countless manufacturing applications where pipes, hooks, castings and a variety of other equipment components are made.
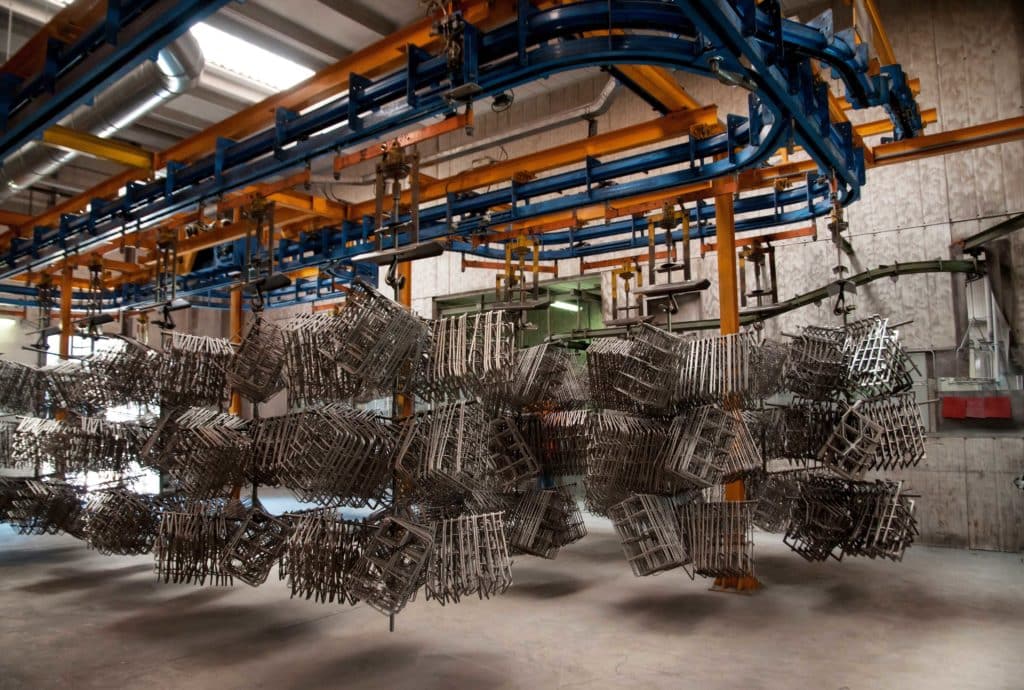
Fast-paced manufacturing applications are the number one candidate for EcoShield 386 FD
- Extra slip applications
Electrical conduits are a prime example of where EcoShield VpCI-386 HT Slip Coating is beneficial. A protective inner diameter coating can be critical for new piping stored outdoors or shipped through harsh, corrosive conditions. However, when it comes time to install the conduits, electrical wires must be able to slide easily through the tubing. EcoShield VpCI-386 HT Slip Coating makes this possible whilst also inhibiting corrosion.
The same benefits would apply to other metal surfaces, parts or equipment in need of a protective coating that is slippery.
- High temp applications
In addition to needing extra slip, electrical conduits are a great illustration (although by no means the only example) of a high temp application. These pipes start out as flat pieces of metal that are rolled into tubes, welded, and internally painted before the welding heat can cool down. EcoShield VpCI-386 HT Slip Coating was designed to withstand this extra heat during coating application and similar high heat curing processes. It can also be used on equipment that may reach temperatures up to 500°F (260°C) during operation.
The main purpose of Cortec Coatings is to protect metals from corrosion. However, when special requirements such as force-drying, extra slip or high temps enter the equation, Cortec is ready to make the solution fit the need.