Offshore wind foundation protection
A review of typical protective anticorrosion coating technologies used on fixed and floating offshore wind tower foundations that are qualified by leading performance standards such as Norsok M-501, by a team from PPG Protective & Marine Coatings.
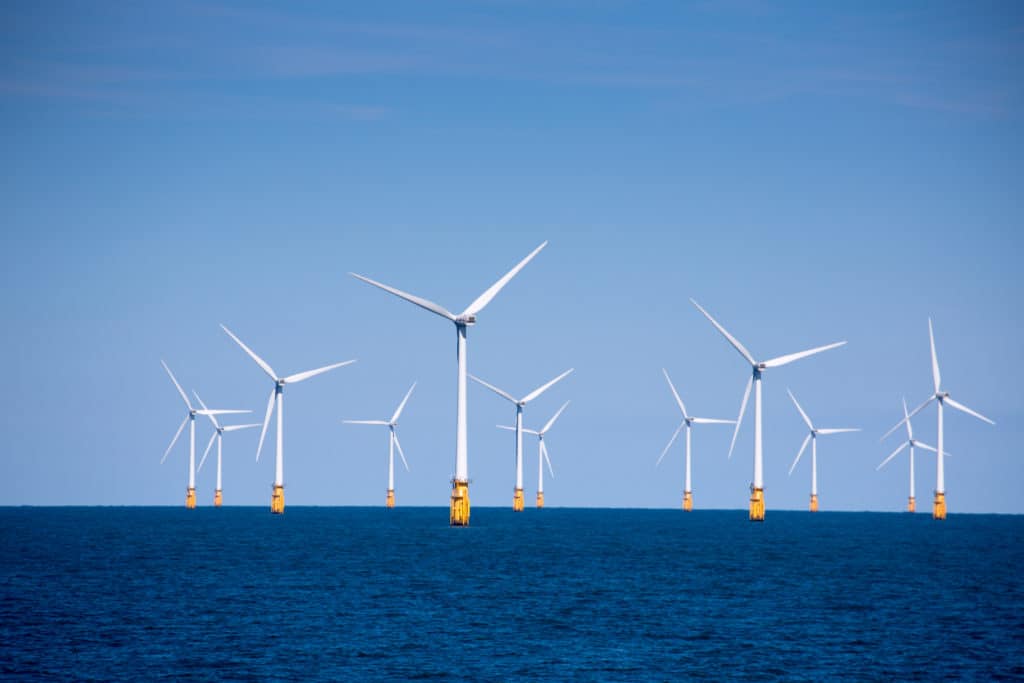
In 2021, of the total 830 GW of wind capacity installed, only 7% were offshore wind farms
As a result of measures to fight climate change, there is a growing need for energy generation from natural sources such as wind and solar radiation. For both energy generation routes, solar and wind, increasing investments are made by governments, energy and operating companies owning and running these installations.
In 2021, of the total 830 GW of wind capacity installed, 93% were onshore systems, with the remaining 7% offshore wind farms. Onshore wind is a developed technology, present in 115 countries worldwide, while offshore wind is at the early stage of expansion, with capacity present in just 19 countries.
Although the installation of large-size onshore wind parks leads to economical electricity production, installing large offshore wind parks has gained enhanced interest because of its higher production efficiency. According to a report from the International Energy Agency, cumulative offshore wind capacity is forecast to more than triple by 2026, reaching almost 120 GW. By then, offshore wind additions are expected to account for one-fifth of the global wind market. Global capacity additions of offshore wind are set to reach 21 GW by 2026, thanks to rapid expansion in new markets beyond Europe.
However, the construction and operation of offshore wind parks bring many technological challenges that need to be overcome to reduce the operational and financial risks of these mega investments. The more difficult installation circumstances, together with the harsh environments to which the wind towers are exposed, are the main challenges to deal with. This requires high-quality construction and protection materials to ensure a prolonged lifetime, together with minimal maintenance, which is difficult and costly.
At present, typical generic coating technologies qualified for fixed offshore wind foundations are either reinforced epoxy- or glassflake unsaturated polyester-based. Both generic coating types have their specific properties and will be further reviewed.
Chemical nature of heavy-duty protective coatings
To understand the application and performance properties of the preferred coating categories, deeper insight into the chemistries is needed. Two-pack epoxy coatings – in this case, so-called high build, solvent-free, two-pack epoxy coatings ̶ are composed of a mix of a low viscous epoxy resin and an amine curing agent. This leads to a dense water-impermeable crosslinked polymer matrix. To further enhance the water impermeability and thus the protective properties of an epoxy coating, so-called novolac phenolic epoxy resins can be used. The resulting coating (for example PPG SigmaShield 1200) has a high crosslink density, which gives it superior mechanical properties such as high stiffness and toughness. The cured coating is also highly resistant to water, solvents and corrosive species, making it ideal for use in harsh environments. Besides the resins used, these coatings are further engineered with mineral or ceramic reinforcement pigments.
The two-pack unsaturated polyester coating is based upon unsaturated polyester resins and cured by minimal amounts of a peroxide catalyst. Adding these catalysts generates an auto-polymerisation reaction whereby the unsaturated polyester polymer partly crosslinks, partly homopolymerises, and solidifies. To densify and fortify the solidified polyester matrix, typically, large amounts of laminar glass flakes are added. It is claimed that using laminar glass flakes reduces the ingress of water into the coating film, providing better corrosion protection of the steel substrate to which it is applied. However, microscopic pictures of glassflake-containing coating films show a rather disorganised random positioning of the glass flakes within the film, and so the added value to the anticorrosion functioning of the coating can be disputed. High loadings of glass flakes also increase the viscosity of the polyester coating, so considerable amounts of reactive diluents like styrene or vinyl toluene are to be added. These diluents have a strong, pungent smell and make the use of polyester coatings less user-friendly. Recently, styrene-free unsaturated polyester glassflake coatings (styrene-free UPE coatings) have been introduced to reduce the strong smell, making the product more pleasant to use.
This crosslinked resin matrix of high-build epoxy coatings also shows, aside from water resistance, excellent resistance against a variety of chemicals such as alkalis and solvents. Particularly in cases where cathodic protection (CP) systems like galvanic anodes or impressed current are used, the alkali resistance of the polymer matrix is critical. The CP systems will generate an alkaline environment by the electric decomposition of water in case of coating damage or failures. Aside from the alkalinity that develops when CP systems are activated, stationary seawater inside the wind tower foundation gradually increases in pH. The higher the pH of the seawater, the more aggressive it is to coating systems, mainly when resin systems are susceptible to such an alkaline water environment. Polymerised polyester resin matrices are known to be less tolerant to alkaline exposure environments due to the ester moieties/building blocks within the resin matrix and so are considered to perform less well in these high pH exposure conditions.
Coating system maintenance
Visual, small damages to the coating systems need to be repaired on a regular basis. Generally, annual inspection routines will identify where such damage has occurred. Where possible, power tooling should be used to remove corrosion and poorly adhering coating. Subsequently, rinsing with tap water is required to remove any salt contamination. This is essential to avoid any osmotic blistering of the coating system at a later stage. It is recommended to use a primer coat suitable to be applied to the power tooled and water-rinsed damaged area (St-2 cleanliness). After primer application and curing, the original coating system can be applied. Between each coat, tap water rinsing should be used to ensure that no soluble salts are embedded.
The above repair procedures onsite at wind tower foundations are quite difficult to execute. User-friendly coating maintenance systems are to be used. Two-pack epoxy coatings and PPG SigmaShield 1200, in combination with the PPG SigmaPrime 200 primer, have such tolerant application properties. Suitable alternative coatings (for example PPG SigmaShield 880), fully qualified for offshore wind tower foundation maintenance procedures, can also be used. Unsaturated polyester coatings are less application-friendly for on-site maintenance procedures. Tuning the mixing ratio with the low amounts of peroxide catalyst and the resulting short pot life makes manual application under these difficult application conditions hardly possible. Alternative coating repair systems probably need to be used.
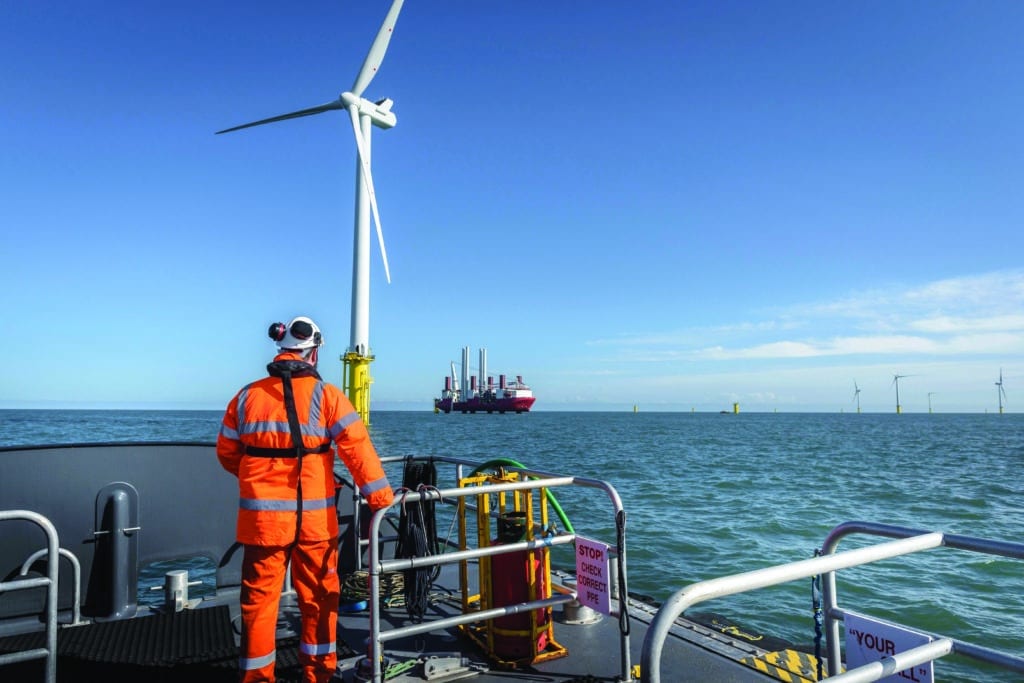
Repair procedures onsite at wind tower foundations are quite difficult to execute
Lifetime expectations of heavy-duty coatings
The splash/tidal zone is most susceptible to corrosion due to paint system damage or failures. Still, owners and operators would like to rely upon long-term flawless corrosion protection with minimal coating system maintenance.
To provide reliable lifetime projections, the frequent successful use in the shipping and oil and gas industries is a good indication of the excellent protection properties of the PPG SigmaShield 1200 coating system. Track records of multiple vessels and oil and gas installations confirm that after 10 years or more in operation, minimum maintenance is required. Even with ice-going vessels, this coating system shows excellent corrosion protection and outstanding impact damage resistance. The suitability of PPG SigmaShield 1200 for wind tower foundation protection is further supported by full compliance with Norsok M501- System 7A performance requirements.
But how can the industry establish reliable data for longer lifetime expectations, such as 30 years+, as frequently demanded in the offshore wind tower industry? For insight into such lifetime expectations, Electro Impedance Spectroscopy (EIS) testing is most suitable. Accelerated testing and focusing on the eventual degradation of the impermeability function can be monitored. When there is little or no change in impermeability after runs of accelerated testing, extrapolation can be made to the real-life performance of the coating system. Such EIS testing of the PPG SigmaShield 1200 system (2x 500µm) has been performed by the independent test institute C-Cube International. After 585 days of exposure to 5% NaCl @ 35°C in C-Cube’s tidal cabinet, no signs of any significant coating degradation have been observed.
The EIS measurement data show that the barrier function (BI) after the 585 days of exposure to salt fog, tidal and seawater only dropped about 10% compared to the ideal resistance/insulation behaviour. The permeability of the coating system dropped to minimal or none. The absence of a decline in permeability index (PI) confirms that the coating displays no signs of degradation during the extended test period of 585 days. This allowed C-Cube to conclude a lifetime projection of the PPG SigmaShield 1200 coating system: “Based on extrapolation of the ISO 12944-9 (CX+IM-4) test duration, the system PPG SigmaShield 1200 @ 2x 500 micron is expected to have a technical lifetime of 50 years or beyond.”
Application process
Critical for realising a long-term anticorrosion system is secure substrate pretreatment in combination with a correct and high-quality application process of the right heavy-duty coating system.
A grit-blasted surface cleanliness of ISO Sa 2.5 with a minimum surface profile of 50-100µm is required. Soluble salt presence should be avoided and not exceed 20mg/square metre as specified in Norsok M-501 and in wind farm project specifications. Once these substrate requirements are fulfilled, the paint system will show excellent adhesion performance. Moreover, the minimal presence of soluble salts prevents osmotic processes that could lead to blistering and coating detachment occurring under humid or immersed conditions.
Offshore wind foundation coatings systems are typically specified as two-coat systems. So, easy and fast re-coatability of the cured first coat is essential to minimise hold-ups in the production process of the wind tower foundations. Here another shortcoming of unsaturated polyesters is being reported. For unknown technical reasons, the inter-coat adhesion of the second applied unsaturated polyester coats can be poor. In order to correct the occurrence of the variable inter-coat adhesion, the surface of the first coat needs to be pretreated; for example, by mechanical disc sanding. It is a time-consuming activity and increases the application costs for the realisation of a full two-coat system. Two-pack epoxies like PPG SigmaShield 1200 show, when applied under the right indoor conditions, no problems in adherence between two coats and without any additional pretreatment of the first coat.
Finally, care should be taken with leftovers of mixed unsaturated polyester coatings. The vigorous reaction speed may develop very high in-can temperatures that may lead to self-ignition and therefore risks of fire. The coating suppliers typically recommend adding water to the leftover cans to avoid the fire risk. Clearly, good training and discipline of the application team is required to realise safe coating leftover disposal management.
Summary and conclusions
Offshore wind tower foundations are exposed to extremely harsh environmental and corrosive conditions. For this reason, high-quality, very durable coating systems are to be used at the time of the new building. Moreover, any on-site maintenance and repair of the coating system is difficult and costly.
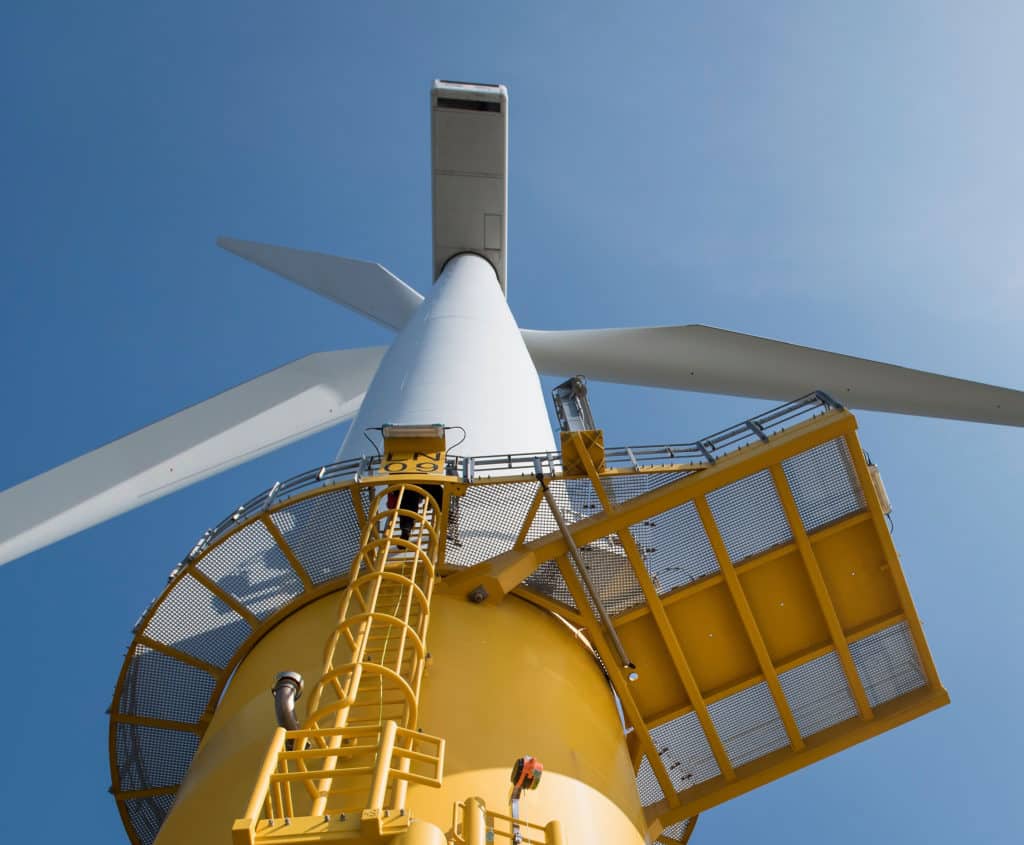
Heavy-duty reinforced epoxy coatings, such as PPG SigmaShield 1200, have long-term and extensive successful track records in a variety of marine exposure conditions, identical to those of offshore wind tower foundations
Heavy-duty reinforced epoxy coatings, such as PPG SigmaShield 1200, have long-term and extensive successful track records in a variety of marine exposure conditions, identical to those of offshore wind tower foundations. As such, PPG SigmaShield 1200 will provide excellent corrosion protection over the projected lifetime of these foundations and is therefore preferred over unsaturated polyester or recently-introduced styrene-free UPE coating technologies. Also, the application of unsaturated polyester coatings is less user-friendly compared to epoxy-based coatings. This provides higher risks of coating system imperfections and thus a higher chance of unforeseen costly maintenance and repair procedures. All these aspects should be considered by wind farm stakeholders when selecting anticorrosion coating systems for offshore wind tower foundations.
The full article can be found here:- https://www.pce-international.com/research-and-development/
Authors: C Y Lee, PPG Global Product Support Manager for Protective & Marine Coatings (PMC), Kent Holm, PPG Global Wind Power Segment Manager for PMC; Ronnie Peskens, PPG Global Product Manager for PMC, Eric King, PPG Global Segment Manager, Powder & Mining, for PMC and Gerard Geels, PPG Senior Product Specialist for PMC.