Transformer protection upgrade
Transformer manufacturers are facing many challenges: the looming winter storm season, supply chain challenges, labour shortages and more. Whilst many factors are beyond their control, identifying paints and coatings that offer next-level protection for important metal components is within their purview, explains Maria Lamorey, Commercial Strategy Manager, PPG.
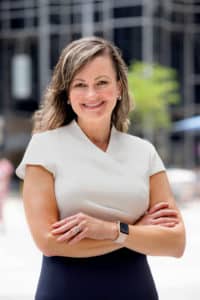
Maria Lamorey, Commercial Strategy Manager, PPG
Considering a transformer’s exposure to extreme weather conditions, outdated and substandard coatings systems can — and do — lead to impairments and disruptions in power services. The right coating system that offers durability and resilience at every layer of protection can extend the service life of transformers and reduce the risk of coatings-related failures — a move that helps to protect their business and their brand. It all starts with a detailed and up-to-date paint specification.
Strong defence against corrosion
When it comes to the metal components of a transformer, corrosion is Public Enemy Number One and prevention is the top line of defence.
Metal electrical equipment parts corrode for any number of reasons. Some factors include the intersection of two metals with different corrosion thresholds; continuous or repeated exposure to high temperatures and humidity from decades in the field, and damaging acidic pH levels, electrolytes, chemicals and ultraviolet rays from sunlight.
Coatings specification: the building block of better protection
If the goal of an electrical equipment manufacturer is to build next-generation components that exceed performance mandates while protecting its brand reputation, paint specifications should be reviewed and updated regularly.
Selecting the right coating system and a supplier that utilises advanced formulations will help transformer, switchgear and other electrical equipment manufacturers outperform competitors, extend the lifecycles of their products and reduce warranty claims.
On average, finished electrical components are composed of about 70% metal and 30% non-metal substrates. Yet despite the importance of high-quality protective coatings in terms of durability and performance of their goods, most electrical equipment manufacturers view painting metal as beyond their core competency.
Whilst most electrical equipment holds a minimum life expectancy of 20 years, many components are expected to survive 50 years or more. Harsh elements can accelerate corrosion and leave sensitive instrumentation vulnerable during storms and compromise its reliability.
Unfortunately, many manufacturers still combine old “cut-and-paste” specifications that date back 20-30 years with current industry-standard regulatory requirements written by IEEE, UL, CSA and ASTM when painting and protecting new equipment.
Coatings manufacturers can contribute to the problem by relying on standards dictated by their customers, or by taking the path of least resistance and continuing with existing solutions instead of exploring more advanced technologies that are proven to perform better in the field.
The foundation of any great coatings system starts with the right specifications.
Read more in the latest issue of Protective Coatings Expert